Interview with Debjit Chandra, Global Technical Service Manager for Dorf Ketal
How does Dorf Ketal differentiate itself from other specialty chemical suppliers in the industry?
Refineries use specialty chemicals to improve the process efficiency, safety, and sustainability of the refining process. The specialty chemicals industry is highly competitive with global companies that dominate the market. Dorf Ketal is the newest entrant. The economic benefit of specialty chemicals on the total cost of operation far exceeds the cost of the chemicals.
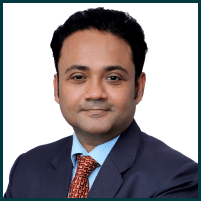
Global Technical Service Manager
Dorf Ketal
Total cost of operation is a combination of tangible cost benefits such as reduced fouling and corrosion and optimization of chemical costs, and intangible costs such as improved sustainability, safety, more capable service representatives, better training of operators, reliabiility and quality of chemical supply, and increased ability to manage process variability. We differentiate by offering our customers sustainable solutions that deliver lower total cost of operation than alternative chemical suppliers.
What unique value do you bring to your customers?
Refiners have successfully used competitive bidding to minimize chemical cost differences. Decisions to change suppliers are most commonly driven by offering a solution to correct a problem or helping the refiner take advantage of the opportunity to reduce costs by widening the crude slate options that can be processed. Dorf Ketal has risen up the ranks to top tier chemical solution provider through consistently exceeding refineries expectations through creating value “beyond acceptable KPI”. We offer excellent line item chemical costs, but this is generally not sufficient to drive change and gain market share as the cost of a problem in managing specialty chemicals can far exceed chemical cost savings by changing suppliers. The strategy Dorf Ketal has used to gain market share, is innovation in patented technologies, that delivers superior value over old technology options used by the industry. In addition, we have innovated on service models to help our customers quantify the increased value.
How is Dorf Ketal incorporating sustainability into its product development and manufacturing processes? Can you share examples of sustainable solutions?
We take a broad measure of sustainability – reduced energy costs, reduced carbon footprint, and improved safety, the list goes on. It is also superior total cost of operation that is a necessity to meet the business requirements for economic sustainability of the business in a changing world. In this conference we presented a paper on how patented innovations in desalter chemistry meet the needs for lower total cost of operation and improved sustainability. Our patent portfolio is most relevant to the hydrocarbon industry fraternity and directed towards contributing to the sustainable goals. Without patent protection, our approach to reducing total cost of operation could be copied by other suppliers and they would have done this to stop us from taking their business. In manufacturing, our sustainability report is detailed and extensive and is available on our website.
What are the primary challenges refineries are facing today, such as feedstock flexibility, product quality, and environmental regulations? How do Dorf Ketal’s products address these challenges
We believe reducing energy costs and carbon footprint drive the efforts of upstream and downstream hydrocarbon industry. Dorf Ketal has recently introduced finished fuel additives that deliver a higher standard of product quality in energy efficiency. Through our innovation, the hydrocarbon industry has accrued tangible reduced GHG emissions, reducing the oil losses in the refineries, decreasing the utilities – steam consumption, increase the production efficiency and quantifiable energy savings. The automotive industry through our Fuel Efficiency Improver ( globally commercialized by oil majors ) has seen significant CO2 reduction/emissions control.
Given the growing demand for petrochemicals, what are the key trends driving this growth? How is Dorf Ketal positioned to support this expansion?
We approach the petrochemical market with the same innovation strategy. Just as in refining, the decisions to change suppliers are most often driven by an unsolved problem or an opportunity to optimize on their Total cost of operations with increased energy savings. A general need here is extending run-length, this is a primary reason for our success using differentiated fouling control chemical technologies for ethylene, butadiene, and styrene. Most recently we have introduced a new safer sulfiding agent for ethylene that improves run-length and furnace yield.
How is Dorf Ketal contributing to the energy transition and supporting the development of low-carbon technologies?
Dorf Ketal has introduced new fuel additive technologies that improve fuel effiency and reduce particulate and CO2 emissions. Our product technologies reduce the carbon footprint of our customer operations. We have developed metrics to allow quantification of the carbon intensity of our products and the value it gets to our customers in the hydrocarbon industry.
What motivated Dorf Ketal to be part of the event this year? Are there any aspects or sessions that you are particularly excited about?
Dorf Ketal looks forward to networking with the oil companies and understanding the latest trend in the hydrocarbon industry. Reducing energy costs through innovation and sustainable fuels are key sessions we are looking forward to.
Tell us a little about what we can expect to see or hear from you at the event this year.
Dorf Ketal has contributed to the hydrocarbon industry through the innovations in reducing the energy costs and carbon footprint, thereby creating value for our customer in the hydrocarbon industry. We would like to showcase these achievements during the event. We would strive towards excellence through understanding more on the unresolved industry challenges to continue our innovation drive.
About the interviewer:
Debjit has more than 15-year experience in Refinery and Petrochemical applications. He has worked in India and Middle East countries. He has worked in Technical Sales and Service roles and has been associated with providing trouble-shooting solutions to multiple Refineries and Petrochemicals in India and Middle East including the World Largest Refinery and Off Gas Cracker. Currently, he has been working in the Technical Services role supporting Asia Pacific and Europe Accounts in terms of KPI compliance, continuous improvement, and technical recommendation for delivering value additions. His Area of expertise includes implementing chemical solutions targeted to meet customers Key Business drivers viz. = Improving Asset Reliability, Profitability and Sustainability.