A guide to industrial AI and digital transformation
Written by: Jonas Berge, Senior Director of Applied Technology, Emerson
The scope of automation in refineries, petrochemical complexes, and other plants today is much broader than just core process control. Now it includes improving safety, sustainability and reliability – over and above production – as plants must achieve operational excellence, without increasing their workforces. The scope of industrial automation and control systems (IACS) includes distributed control systems (DCS), safety instrumented systems (SIS), machinery protection systems (MPS), manufacturing execution systems (MES), and energy management information systems (EMIS) just to name a few. Industrial artificial intelligence (AI) plays an important part in all these automation and control systems to support production and maintenance, but also in the deployment of the automation and control systems themselves.
Industrial AI Tools
The technologies used in these industrial AI tools fall into four broad categories: causal AI, machine learning, deep learning, and generative AI (GenAI). It should be noted that none of these are better than the others for all tasks, just like a hammer is not better than a spanner for all jobs. Each AI technology has specific strengths and suitable applications:
- Causal AI embeds already well-established first principles of physics and chemistry into models showing how processes and equipment work and embeds already well-known cause and effect relationships describing how they fail into ‘agent’ functions. These types of models and agents are built into readymade apps that quantify efficiency and predict problems.
- Machine learning in its training phase uses one of many statistical algorithms and applies it to historical data from the plant, such as process history, maintenance records and lab results, to find correlation for normal operation and abnormal conditions like failure, process upsets, and quality issues. In the operational ‘inference’ phase, these correlations are then used in agent functions to predict abnormal conditions. There is also deep learning, which is a subset of machine learning based on neural networks.
- Generative AI uses large language model (LLM)-type artificial neural networks (ANN), such as generative pre-trained transformers (GPT), which are statistical algorithms. These systems are pre-trained on existing software code to generate new code based on prompts.
Improving Production and Quality
Industrial AI supports production operations. For instance, by way of a ‘chat,’ an operator of advanced process control (APC) software can ask a ‘copilot’ what controller setpoints to set to meet a certain target like feed rate, and the copilot will respond to the operator with a few options to choose from. Instead of only using traditional simulation tools to try out different settings before applying them to the APC, the user interface is now a conversational assistant with natural language input and response. It involves ‘talking’ to the copilot instead of doing most of that work.
Or a planner can ask the ‘copilot’ of the planning and scheduling software to explain the rationale of marginal values and constraints given by the software model. A third example is deploying dynamic optimization across multiple process units by combining machine learning with causal AI, including first principles models.
These are just a few examples of what industrial AI solutions are capable of today. Industrial AI runs on data, however, so plants need new automation paradigms to enable it. This includes better integration of DCS, SIS, MPS, MES and EMIS, as well as wireless sensor network infrastructure, to automate manual data collection such as vibration, ultrasonic thickness, temperature, pressure, fluid level, and acoustic noise.
Streamlining Maintenance and Reliability
Maintenance is another area where industrial AI can improve efficiency and reduce costs. This includes predicting equipment maintenance requirements to avoid failure, and pinpointing equipment fouling and losses to avoid overconsumption. It can also be used to optimize cleaning and replacement schedules, pinpoint and control emissions, and quantify corrosion rates to better manage corrosion inhibitor injection and pipe section replacement. Again, encoding cause-and-effect subject matter expertise is crucial.
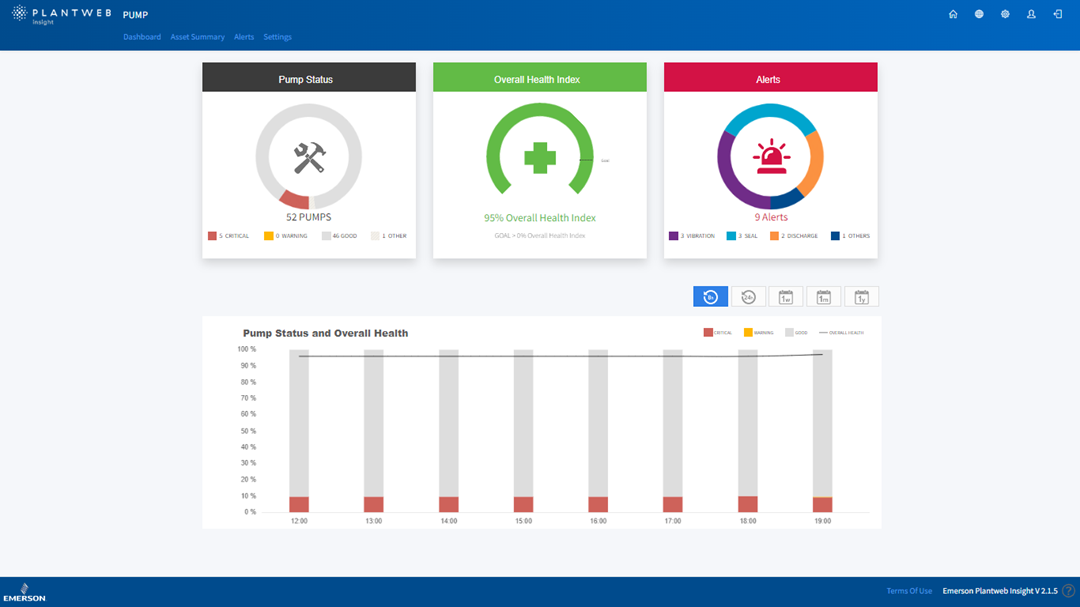
AI not only runs on servers on-premises and in the cloud but also embedded in intelligent field instruments. For instance, smart valve positioners use embedded causal AI to predict the failure of valve assembly components, and first principles AI models to quantify valve issues such as friction and deadbands affecting control loop performance.
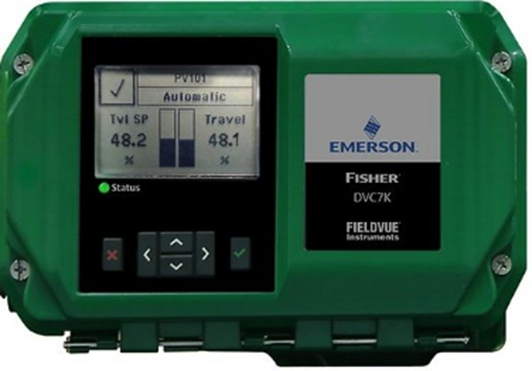
Asset monitoring is another way causal AI embedded in intelligent field instruments can help improve the efficiency of maintenance operations. Causal AI is used to predict problems in fans, motors, gearboxes, pumps, and other rotating machinery so that corrective action can be taken before they lead to failures and unplanned downtime.
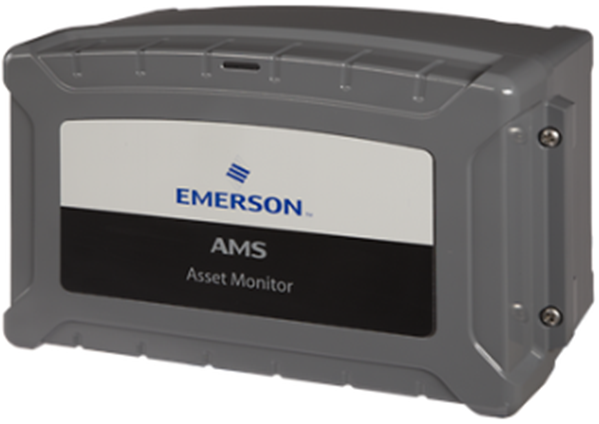
DCS Configuration and the Industrial AI Toolbox
Industrial AI can also be used to support the configuration of DCS. For instance, AI is often used in plant modernization projects when migrating from a legacy DCS and PLC system to help explain the old system’s configuration database and generate an equivalent database for the new DCS. Trained on several legacy DCS and PLC systems, a combination of rule-based AI, machine learning, and generative AI can be used to achieve automatic conversion of up to 70% of the DCS configuration.
Lastly, the hallmark of a good craftsman is the ability to select the right tool for the job. Industrial AI is no different. A plant needs many AI tools in their toolbox because no AI tool is right for every job. Causal AI, machine learning, and generative AI each have their own ideal use cases. A vendor with only one type of industrial AI tool will tend to force-fit that tool into all applications, like a “hammer in search of nails.” Working with a vendor that supports multiple AI tools can help operators avoid single-tool bias.