Register Interest
Be part of the movement shaping the energy transition in ASEAN’s refining & petrochemicals sector.
Submit Abstract
Call for papers is now open! Present your insights, innovations, and expertise to industry leaders and key decision-makers.

Nominate Now!
Nominations for the Asian Downstream Summit Awards 2025 are now open! Showcase your achievements, establish your company as an innovation leader, and receive the recognition you deserve. Drive the transformation of ASEAN’s refining and petrochemicals sector—submit your nomination today!
Register Interest
Be part of the movement shaping the energy transition in ASEAN’s refining & petrochemicals sector.
Submit Abstract
Call for papers is now open! Present your insights, innovations, and expertise to industry leaders and key decision-makers.

About
Asian Downstream Summit
The Asian Downstream Summit (ADS) is a downstream oil and gas event that brings together senior industry leaders and decision-makers from across the downstream value chain. It focuses on critical issues and challenges, with a strategic emphasis on digitalisation and innovation to drive cost efficiency, and operational excellence. It also highlights best practices in asset management across downstream processes.
Be Part of Asian Downstream Summit 2025
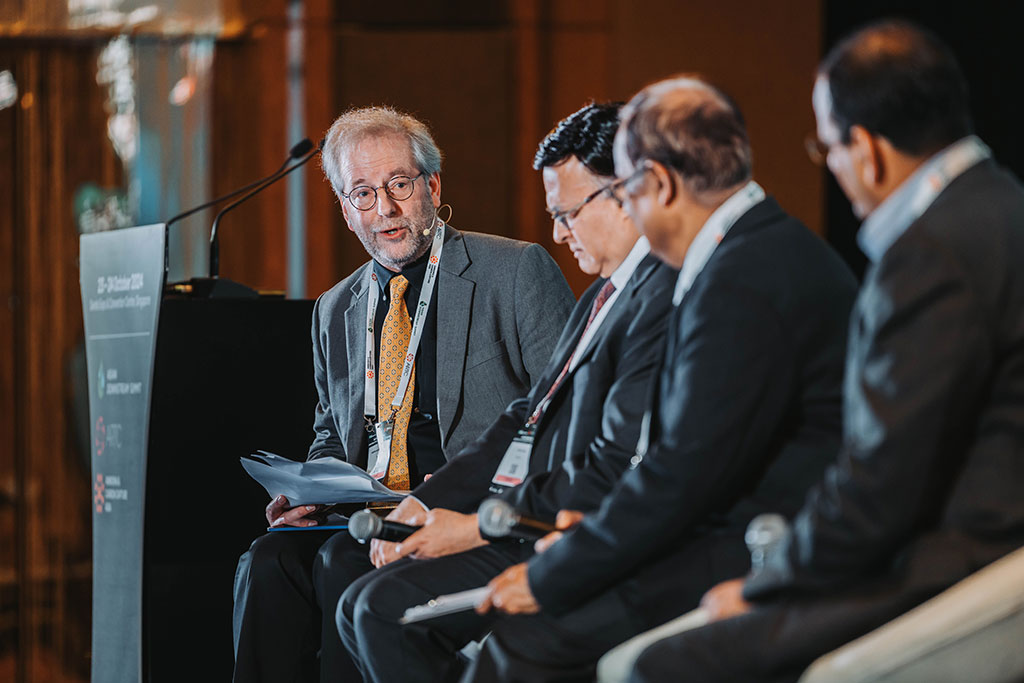
Speak
Share your expertise and shape the refining & petrochemicals future. Register interest in speaking
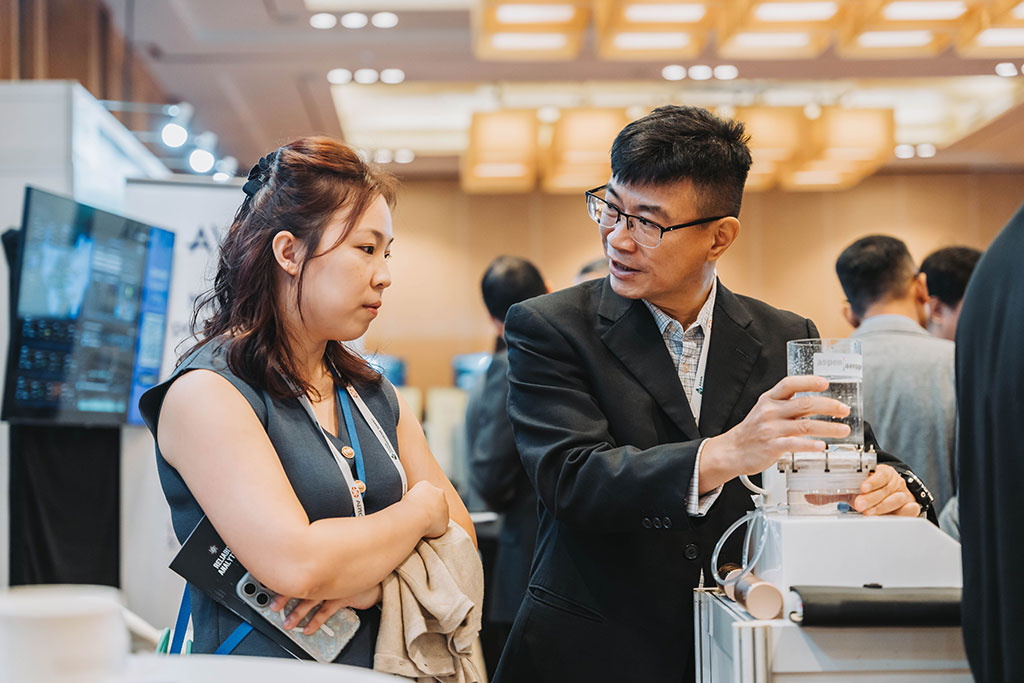
Exhibit
Showcase your solutions to industry leaders from the region. Book a Stand
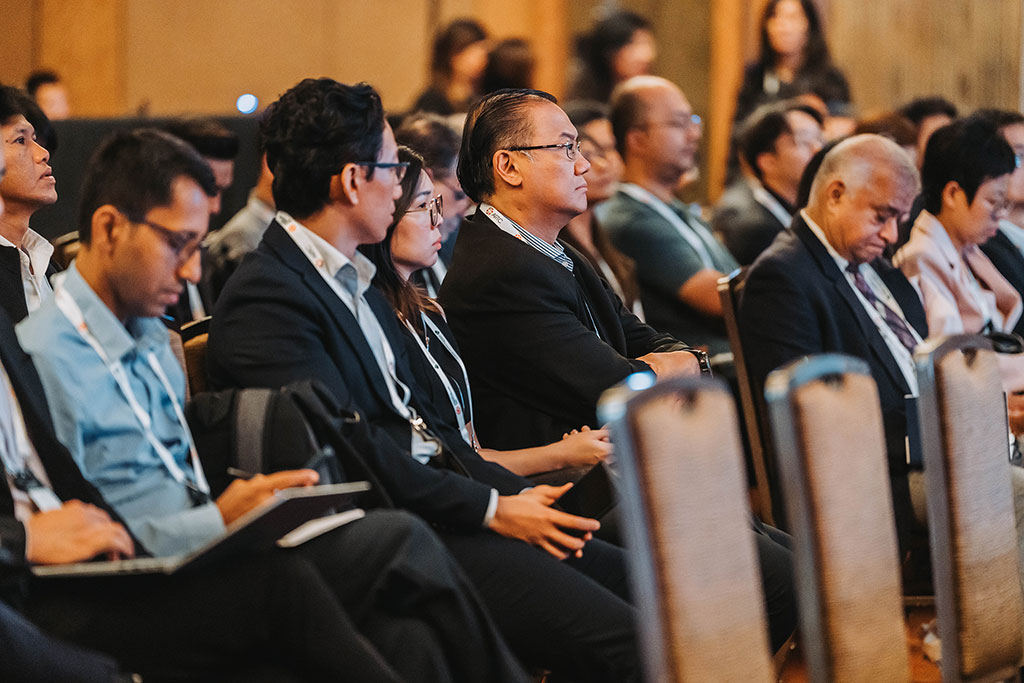
Attend
Register your interest now to be the first to access exclusive early-bird discounts and promotional offers! Register interest in attending.
Who Attends
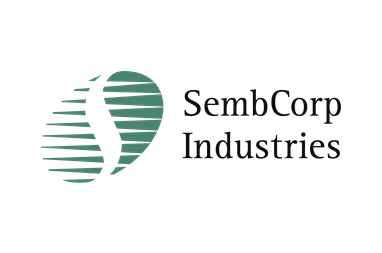
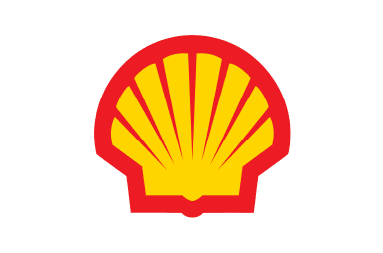
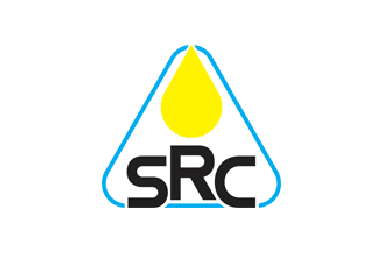
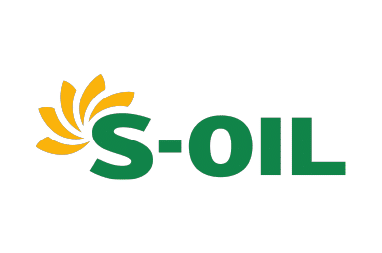
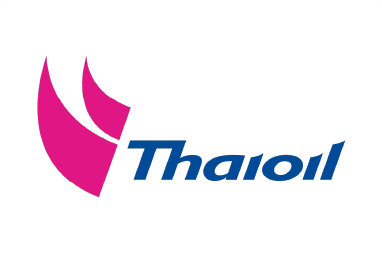
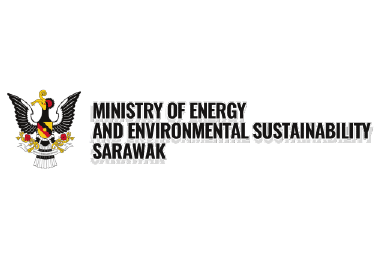
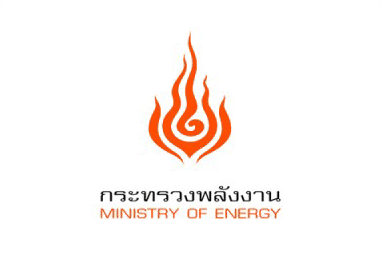
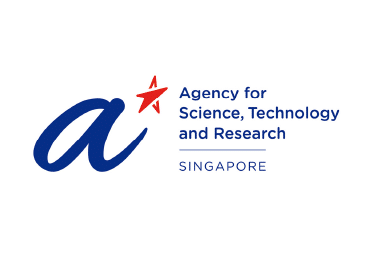
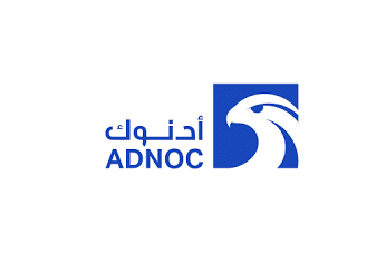
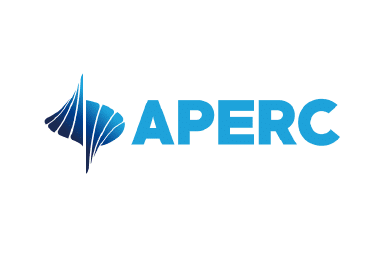
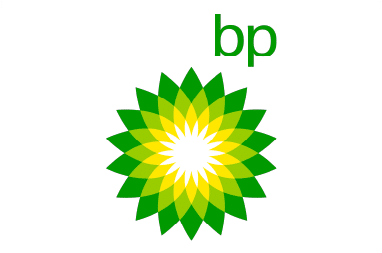
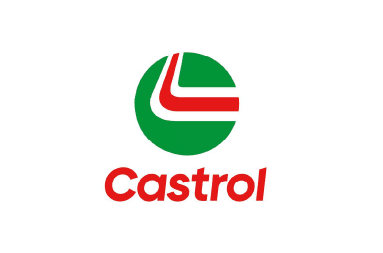
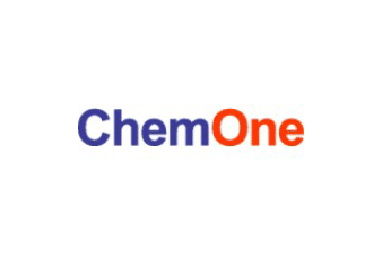
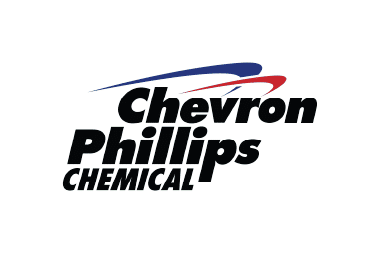
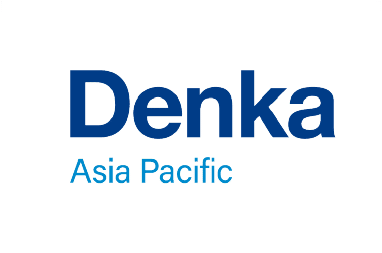
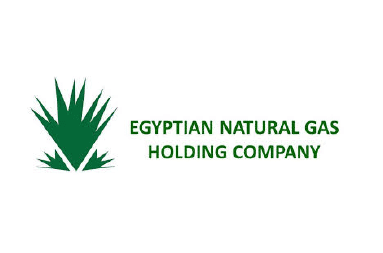
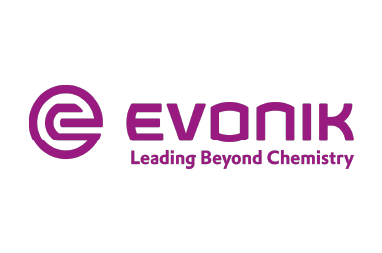
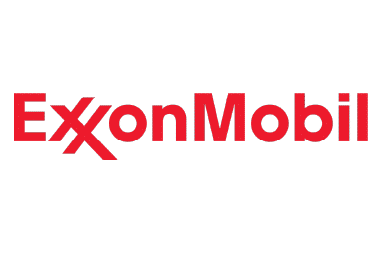
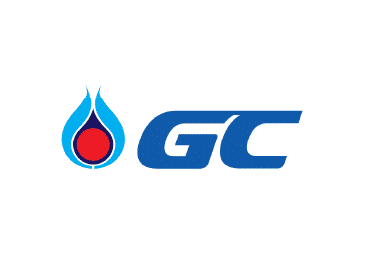
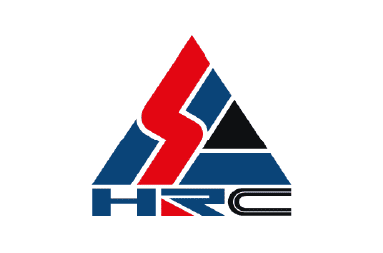
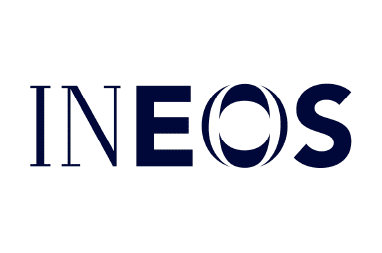
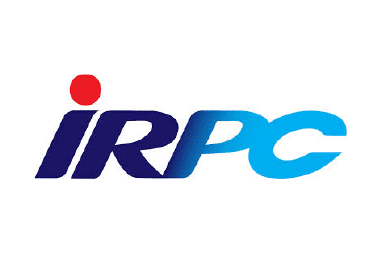
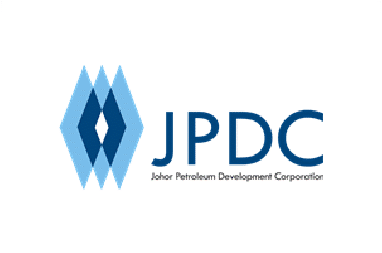

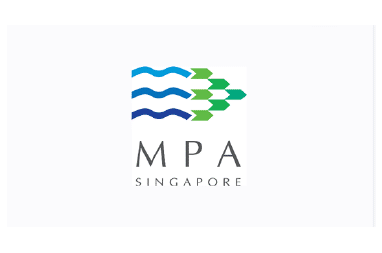
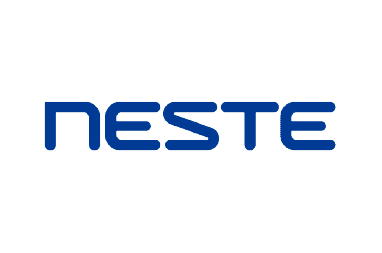
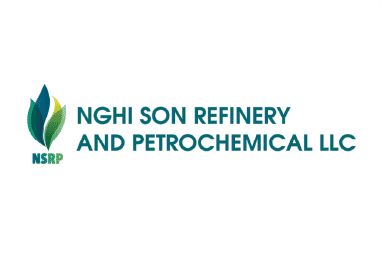
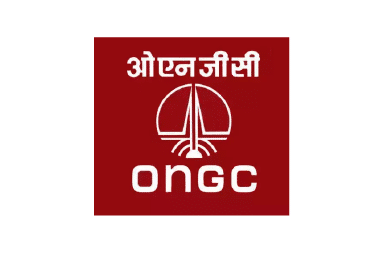

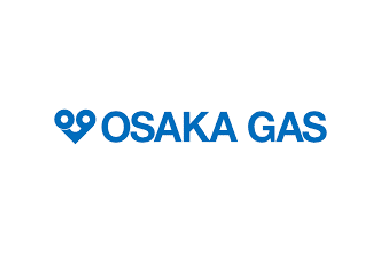
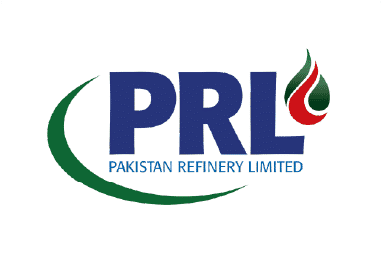
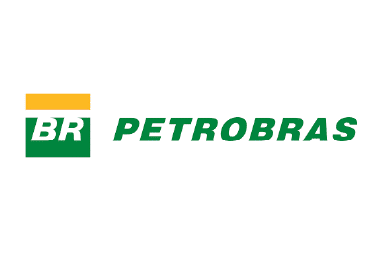
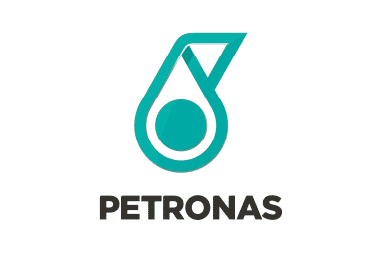
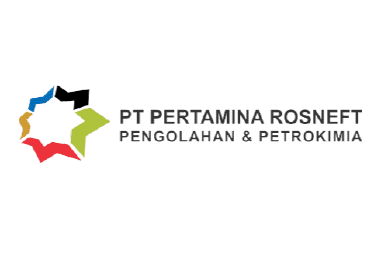
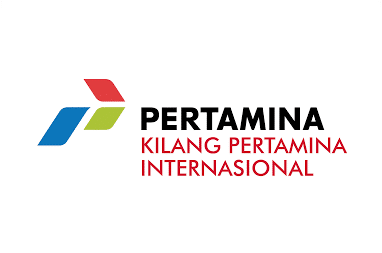
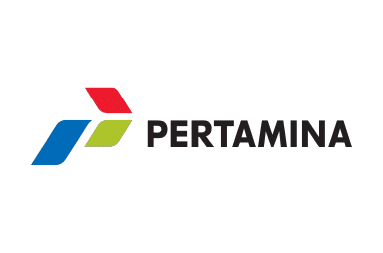
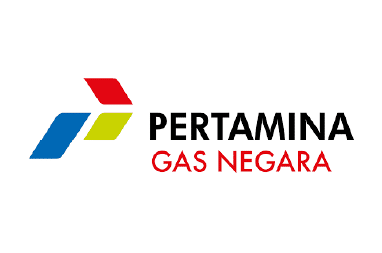
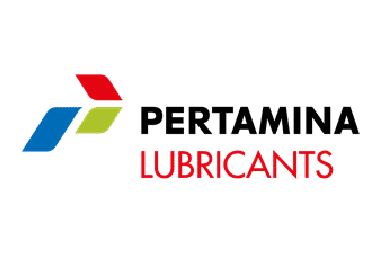
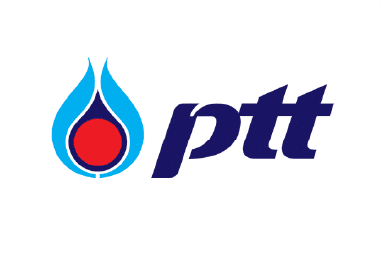
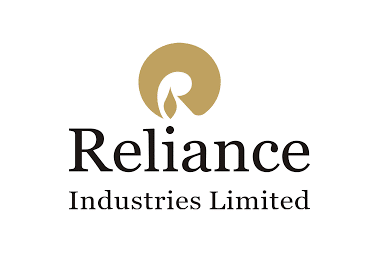
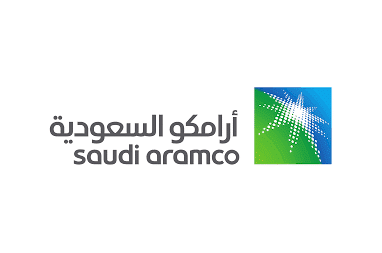
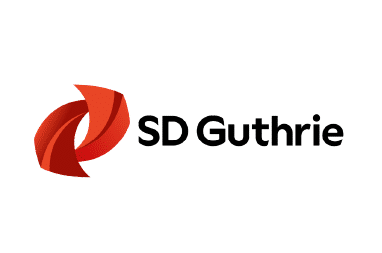
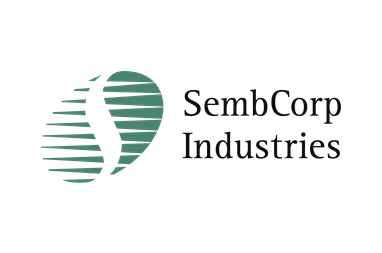
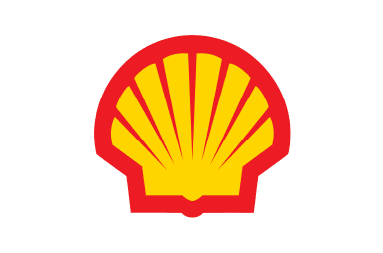
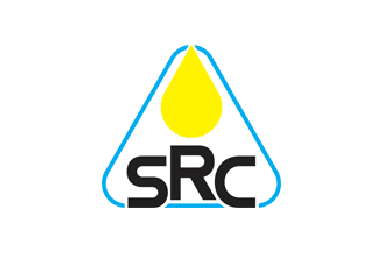
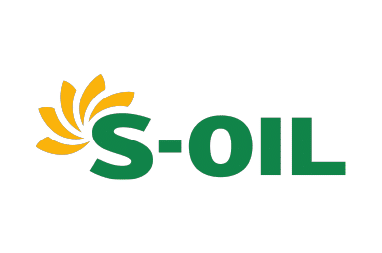
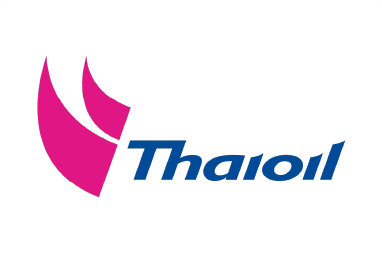
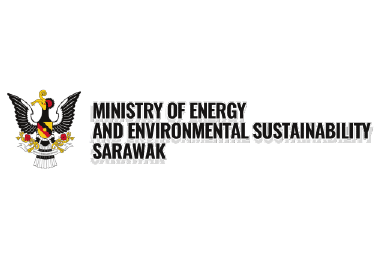
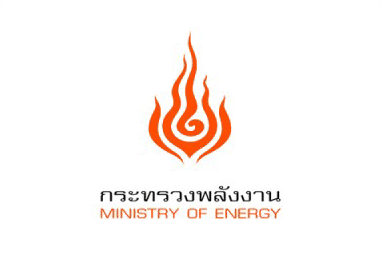
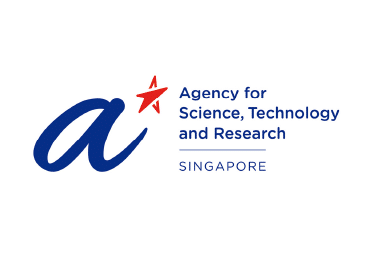
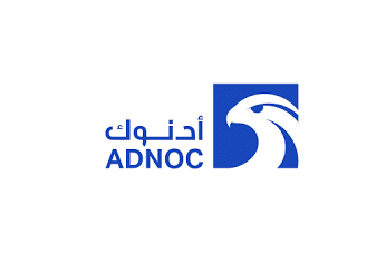
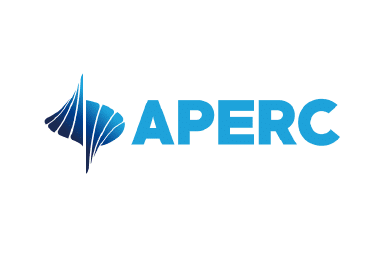